We have had a certified energy management system in accordance with ISO 50001 since 2014. An annual review audit is carried out for this purpose. A recertification audit takes place every 3 years. Our EnMS (energy management system) covers both locations in Lüneburg and Tangermünde and includes all energy sources used.
To implement, maintain and improve our energy management system, we follow the PDCA cycle. The basis for a functioning energy management system is good transparency of energy consumption within the company. For this reason, we have set up over 350 measuring points in recent years, with which we continuously measure and record values and consumption of electricity, gas, steam, compressed air, water and temperature.
All newly installed consumers are directly equipped with measuring devices. With the help of these measurements, we can predict future consumption in detail and align our energy procurement even better.
Based on these energy measurements, we are also able to identify potential energy savings and, after the implementation of energy efficiency projects, to prove their success.
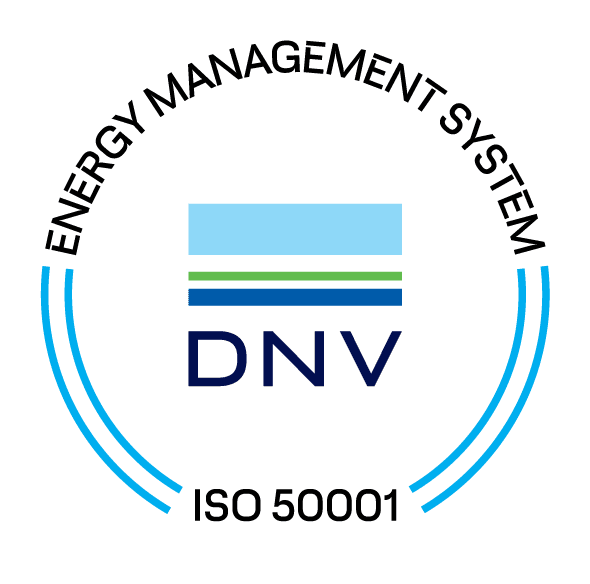
Further implemented Energy Efficiency Measures
- The renewal of compressors including installation and use of heat recovery
- A modernization of the superordinate compressor control
- A successive modernization of production and logistics halls with LED lighting including presence control and brightness sensors
- The replacement of old heating and steam boilers with energy-efficient systems
- A comprehensive optimization of the heating system of the logistics center in Tangermünde including the use of a heat pump
- The replacement of chillers and cooling tunnels towards more efficient models
- The efficiency optimization of the company’s own sewage treatment plant in Tangermünde, among other things, through the use of speed-controlled ventilation motors and process adjustments
- A complete renewal of the forklift fleet with more efficient lithium-ion battery technology ´
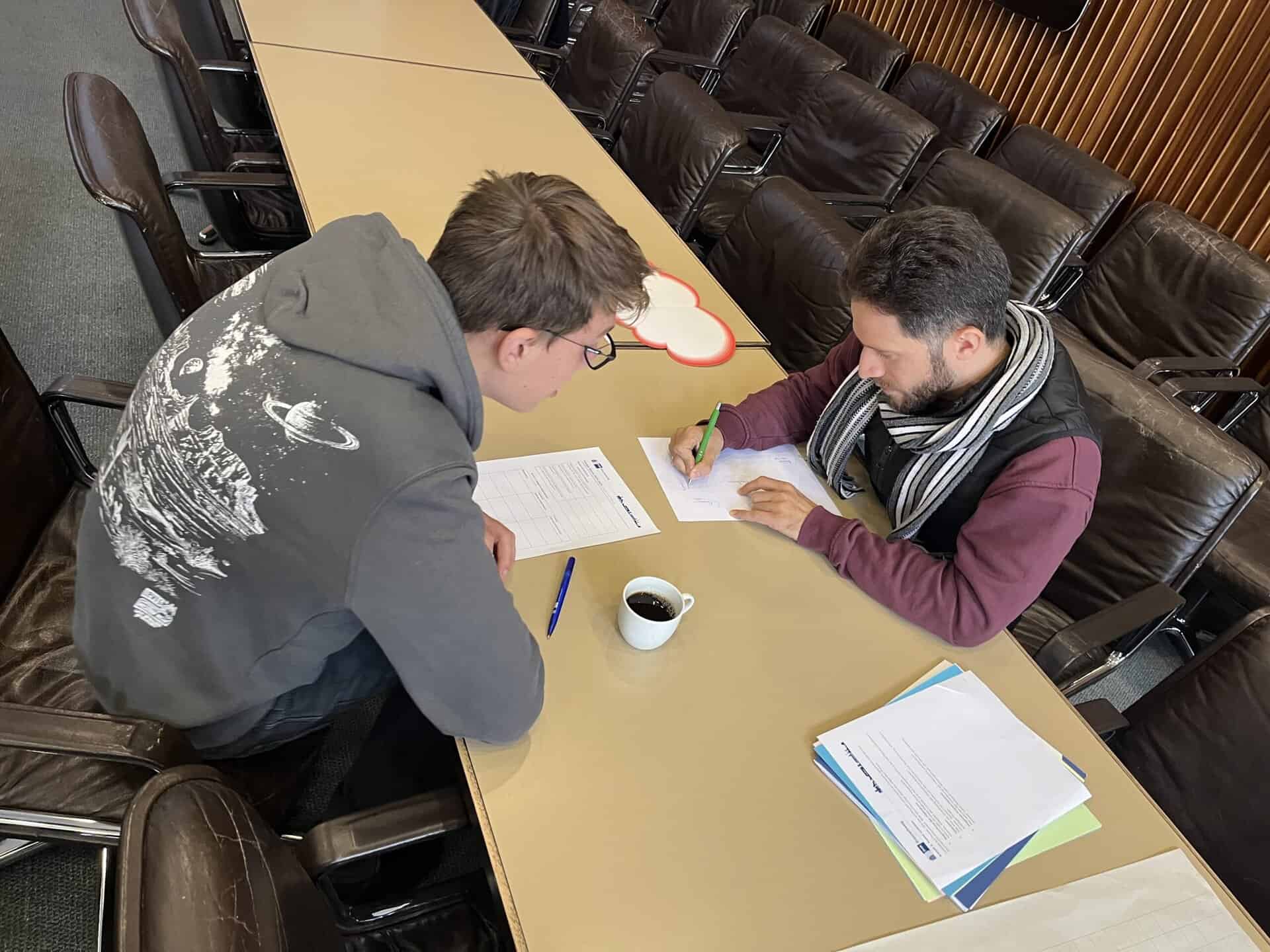
Using Heat – Generating Power: An Energy Scout Project at DE-VAU-GE
In October 2024, trainees Francesco Stagliano and Finn Jasper Hennings took part in the Energy Scout workshop organized by the Chamber of Commerce and Industry of Braunschweig.
Alongside other trainees from the region, they gained practical and detailed insights into energy efficiency, measurement technology, and corporate mobility management.
The aim of the workshop was to raise awareness of sustainable business practices and identify specific energy-saving potential within the company. This potential should finally be exploited.
After an intensive planning phase in January 2025, Francesco and Finn Jasper analyzed the technical requirements, selected suitable materials, and developed a realistic test scenario.
The goal of their project was to convert industrial waste heat into electrical energy using thermoelectric generators (Peltier elements).
Since direct testing on a production plant wasn’t possible due to legal restrictions that couldn’t be resolved during the testing period, they built their setup in a simulated environment.
Using tealights and a cooling pad, they created a targeted temperature difference to demonstrate the functionality of the Peltier elements and collect first measurement results.
With strong support from the technical department, an experimental setup was created that familiarized the trainees not only with metalworking but also with measurement technology and data analysis.
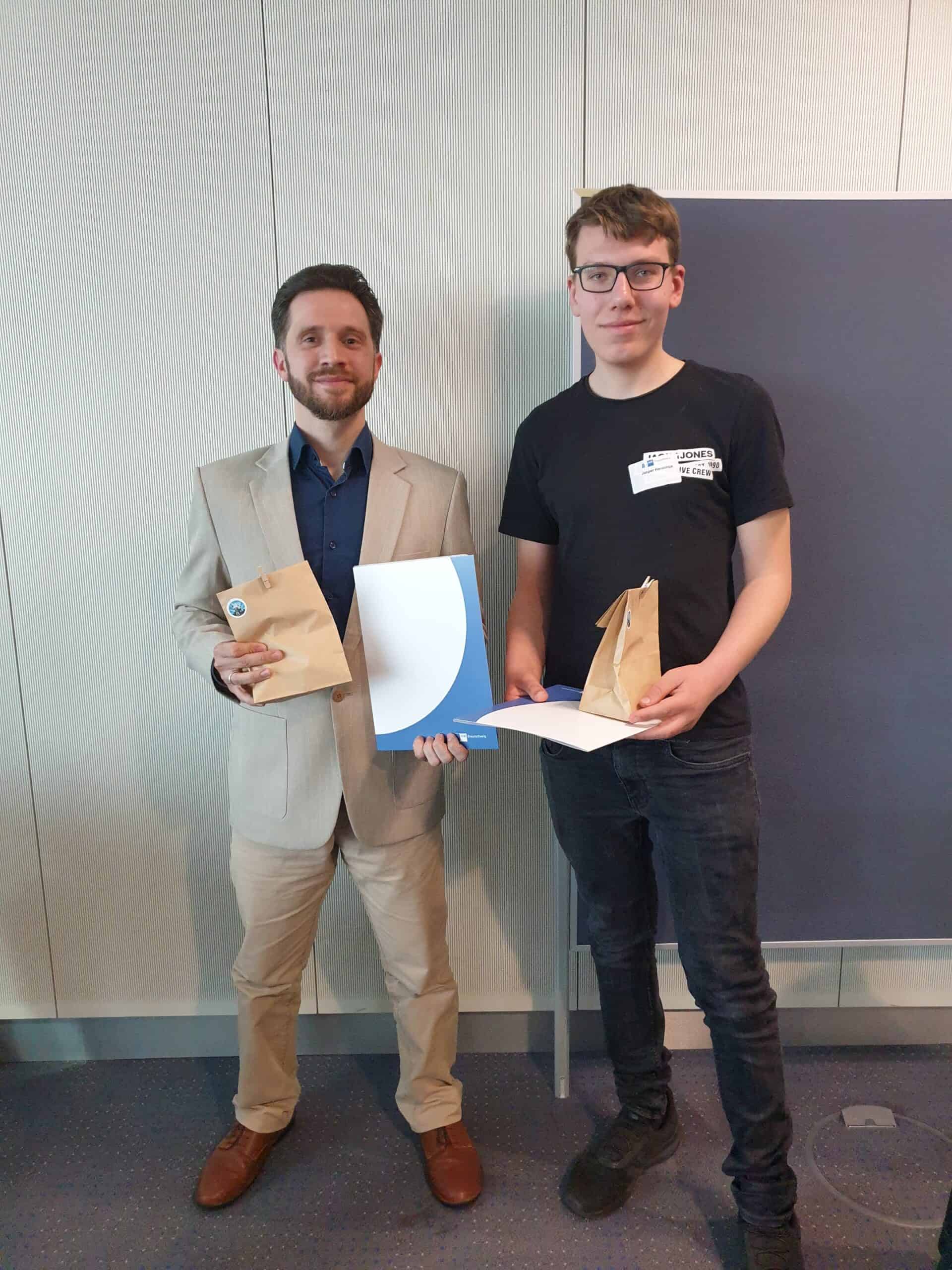
This measurement data illustrates the potential of the concept, particularly as a sustainable addition to industrial energy management. This is a remarkable result for a pilot project by two trainees.
Technical results at a glance:
- Voltage generated: up to 59 volts using ten Peltier elements
- Projected annual power generation: 28 kWh per year
- Potential CO₂ savings: 201 tons per year
- Estimated annual cost savings: €131.82 per year
On March 19, 2025, the two trainees presented their project at the final event of the Braunschweig Chamber of Commerce and Industry in Wolfsburg. With technical expertise, innovation, and a strong sustainability focus, they convinced the jury among 15 competing teams and deservedly took 1st place in the 2025 Energy Scout competition of Braunschweig.
As recognition for their commitment and creativity, Francesco Stagliano and Finn Jasper Hennings were invited to the nationwide award ceremony. This event will take place on June 17, 2025, at the House of German Business in Berlin, honoring Germany’s best Energy Scouts as well as outstanding European Energy Scout projects.